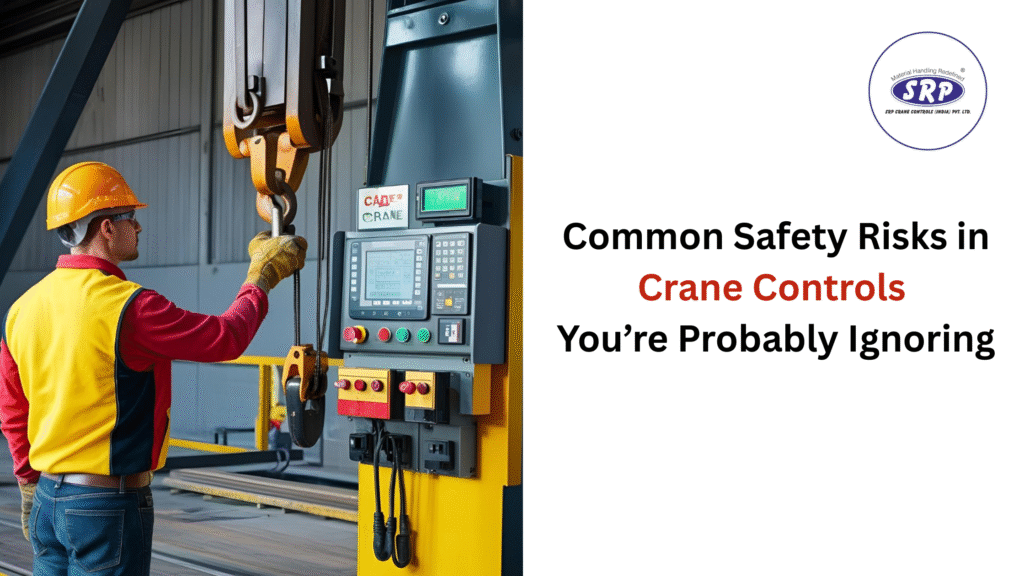
In the bustling world of industrial operations, crane controls are the unsung heroes—or silent saboteurs—of workplace safety. While these systems orchestrate the precise movement of heavy loads, even minor oversights in their design, maintenance, or operation can cascade into catastrophic failures. Consider this: a 2025 HSE report revealed that 22 dangerous occurrences, including crane collapses and jib failures, stemmed from neglected control systems over a seven-year period. Yet, many businesses remain oblivious to the ticking time bombs in their machinery. Let’s pull back the curtain on the risks hiding in plain sight.

Understanding Crane Controls: The Brain Behind the Brawn
At their core, crane control systems are complex networks of hardware and software designed to translate operator commands into safe, efficient movements. Modern systems rely on Programmable Logic Controllers (PLCs) to monitor components like hoists and trolleys, while sensors and feedback mechanisms—limit switches, encoders, load sensors—act as the crane’s “nervous system,” providing real-time data on load weight and positional accuracy.
But here’s the catch: these systems are only as reliable as their weakest link. For instance, a single malfunctioning sensor can misreport load limits, leading to overloading—a hazard responsible for 15% of crane-related injuries. As Ian Simpson, an HSE inspector, bluntly noted after a near-fatal collapse in Croydon: “The circumstances of the accident were virtually the same as at Canary Wharf [in 2000]… yet lessons went unlearned”. This underscores a grim reality: complacency with crane controls isn’t just risky—it’s a recipe for repetitional disasters.
Hidden Risks Lurking in Your Control Systems
Software Glitches: The Silent Saboteurs
While hardware failures often grab headlines, software vulnerabilities pose insidious threats. Outdated PLC firmware, for example, might fail to trigger overload protections or anti-collision algorithms. During a 2024 audit, HSE inspectors discovered cranes operating with decade-old control software, despite known bugs that caused erratic trolley movements. As ports and warehouses adopt semi-automated systems, the stakes rise: a single coding error in path-planning algorithms could send a crane careening into infrastructure—or workers.
Calibration Drift: The Invisible Margin of Error
Precision is non-negotiable in crane operations, yet calibration drift remains a pervasive blind spot. Load sensors that lose accuracy by just 2–3% can nudge operators toward dangerously underestimated weights. In one chilling case, a Newcastle crane’s load cell error led to a 12-ton overload—a mistake only detected after the crane’s structural beams warped irreparably.
“Ghost Commands” in Wireless Systems
The shift toward remote and radio-controlled systems introduces new vulnerabilities. Signal interference or latency in wireless systems can spawn “ghost commands”—unintended movements triggered by electromagnetic noise. A 2025 near-miss in Mumbai saw a container gantry crane lurch sideways due to a stray radio signal, narrowly avoiding a collision with a fuel tanker.

The Domino Effect of Neglected Controls
Ignoring these risks doesn’t just endanger lives—it erodes profitability. The Croydon collapse alone caused £2.3 million in damages and six months of operational downtime. But the fallout extends further:
- Regulatory Repercussions: Non-compliance with ISO 9927-1 (crane inspections) can lead to fines up to ₹20 lakh under India’s Factories Act.
- Reputational Bleeding: A single accident can tank client trust. After a 2024 crane fire in Chennai linked to faulty controls, the operator’s client base shrank by 37% within a quarter.
- Insurance Spikes: Firms with outdated control systems face premiums 15–20% higher than industry averages.
Proactive Strategies to Neutralize Risks
Embrace Predictive Maintenance
Gone are the days of reactive repairs. Smart cranes now leverage IIoT sensors to predict failures before they occur. Vibration sensors on drive motors, for instance, can detect bearing wear weeks in advance, slashing unplanned downtime by 40%.
Upgrade to Fail-Safe Control Architectures
Modern systems like SRP Crane Controls’ dual-PLC setups ensure redundancy: if one controller fails, the secondary unit instantly takes over. Pair this with automatic emergency braking, and you’ve transformed your crane into a self-correcting workhorse.
Train, Then Train Again
Human error accounts for 60% of control system mishaps. Regular simulations—like mimicking load sway in high winds—keep operators sharp. As one port manager in Kochi put it: “We drill until safe responses become muscle memory.”
Innovating Toward Safer Horizons
The future of crane controls is bright—and intelligent. SRP Crane Controls’ wireless radio remotes now feature AES-256 encryption to thwart signal hijacking, while their AI-driven current collectors adjust voltage in real time to prevent arc flashes. Looking ahead, 2025’s smart cranes will integrate digital twins for real-time performance modeling, effectively creating a “crane metaverse” for risk-free testing.
Compliance Isn’t Optional—It’s Survival
Adhering to standards like ISO 12480-1 isn’t just about avoiding fines; it’s about institutionalizing safety. Firms certified under ISO 9001:2015 report 50% fewer control-related incidents than uncertified peers. Regular third-party audits also expose hidden flaws—like the Newcastle-Stoke paperwork mix-up that nearly doomed a crane team in 2024.
The Road Ahead: Cranes That Think
By 2026, expect cranes that “learn” from near-misses. Machine learning algorithms will analyze historical data to predict and neutralize risks—say, auto-adjusting hoist speeds during monsoon rains. As SRP’s CTO recently mused: “Soon, cranes won’t just obey commands… they’ll question unsafe ones.”

Conclusion: Don’t Wait for the Crash
The Croydon collapse wasn’t an anomaly—it was a wake-up call. In an era where a single software bug can topple a tower crane, complacency is corporate suicide. Audit your controls. Train your teams. Invest in systems that think faster than failure. Because in the high-stakes world of crane operations, the best accident is the one that never happens.Ready to future-proof your cranes? Explore SRP Crane Controls’ cutting-edge solutions today—where innovation meets inexhaustible safety.