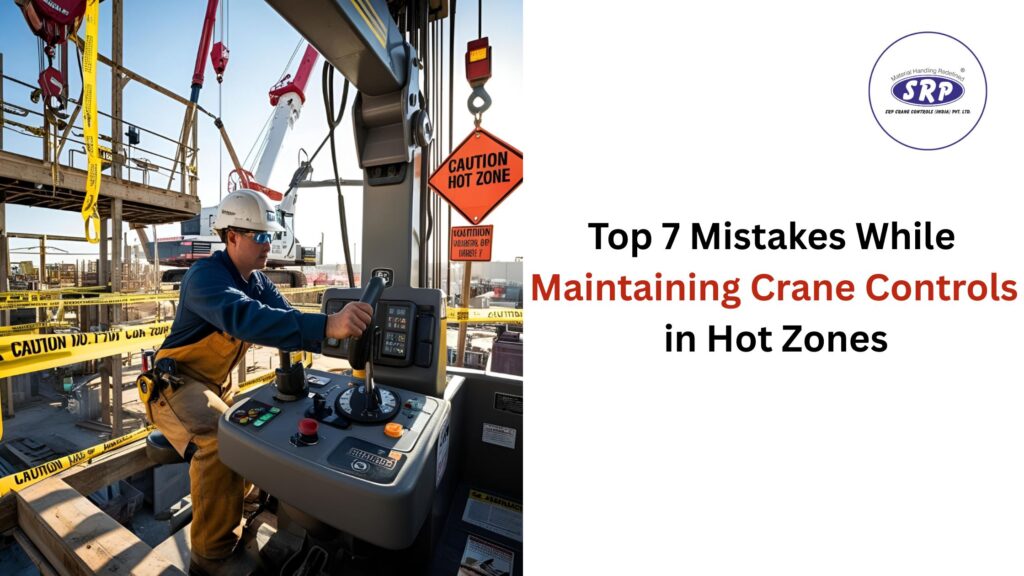
Crane operations in hot zones—where temperatures soar above 45°C (113°F)—are a high-stakes balancing act. A single maintenance oversight can trigger catastrophic failures, from hydraulic leaks to operator errors. With the global crane market valued at $50.75 billion, the margin for error is razor-thin.
This article dissects the top seven mistakes in crane control maintenance under extreme heat, blending regulatory insights, engineering principles, and hard-won field experience to keep your operations safe and efficient.
Introduction to Crane Maintenance in Hot Zones
Extreme heat doesn’t just test human endurance—it pushes crane components to their breaking point. Hydraulic systems, electrical circuits, and load-bearing mechanisms face accelerated wear in hot zones. For instance, O-rings and seals degrade 30% faster in temperatures exceeding 50°C, while steel components expand, compromising structural integrity.
The stakes are existential: A 2023 study by the International Crane Foundation found that 68% of crane failures in hot climates stemmed from preventable maintenance lapses. Yet, many operators underestimate how heat amplifies risks. As one site manager in Dubai noted, “We’d check fluids weekly, but in summer, even daily checks couldn’t prevent leaks”.

Understanding Crane Controls and Safety Protocols
Crane controls in hot zones demand a marriage of precision engineering and rigorous safety protocols. The UK’s Lifting Operations and Lifting Equipment Regulations (LOLER) mandate halting operations when weather “affects the integrity of lifting equipment or exposes people to risks”. This isn’t bureaucratic red tape—it’s a lifeline.
Modern cranes rely on thermal-resistant materials, but even advanced hydraulics falter under relentless heat. Take hydraulic fluid: At 60°C, its viscosity drops by 40%, reducing pressure and increasing pump strain. Without temperature-adjusted maintenance schedules, systems overheat, leading to sudden failures.
Common Mistakes in Crane Control Maintenance
Mistake 1: Neglecting Thermal Stress on Seals and O-Rings
Polymer-based seals, critical for hydraulic systems, become brittle and crack under cyclic heating. A single compromised O-ring can leak 2 liters of fluid per hour, crippling lift capacity. Yet, many teams replace seals only during scheduled maintenance, not accounting for heat-driven wear.
Mistake 2: Skipping Pre-Operation Inspections in Extreme Heat
“If it worked yesterday, it’ll work today” is a lethal assumption. In hot zones, daily inspections are non-negotiable. Cables expand, brake linings warp, and electrical connections corrode faster. One Australian study found that 92% of heat-related crane incidents occurred after skipped inspections.
Mistake 3: Overloading in High-Temperature Conditions
Crane load charts assume “ideal” temperatures. At 45°C, a crane’s rated capacity drops by 12–15% due to reduced structural stability. Overloading in these conditions strains motors and increases the risk of boom collapse.
Mistake 4: Ignoring Hydraulic Fluid Degradation
Hydraulic fluid oxidizes rapidly in heat, forming sludge that clogs valves. As Emerson Crane’s manual warns, “A single degree above 80°C cuts fluid life by half”. Regular viscosity checks and synthetic fluid swaps are essential.
Mistake 5: Inadequate Operator Cooling Systems
Operators in sweltering cabins make 43% more errors than those in climate-controlled environments. Overheating impairs focus during critical lifts, yet many older cranes lack upgraded cooling systems.
Mistake 6: Using Generic Lubricants
Standard greases melt at high temperatures, leaving bearings unprotected. High-temperature lithium-complex lubricants can extend component life by 200 hours in hot zones.
Mistake 7: Delaying Emergency Repairs
A leaking valve or frayed cable might seem tolerable in the short term, but heat accelerates degradation. A minor fault at 8 AM can become a critical failure by noon.

Advanced Insights into Hot Zone Maintenance Challenges
The Physics of Heat Transfer in Crane Systems
Heat radiates unevenly across crane structures. The upper hoist assembly can be 20°C hotter than the base in direct sunlight, creating stress fractures. Thermal imaging cameras are indispensable for spotting these gradients before they cause failures.
Material Science Innovations
New composite alloys and ceramic-coated bearings reduce thermal expansion by 18%, but retrofitting older cranes remains costly. For startups, partnering with specialists like SRP Crane Controls ensures access to cutting-edge materials without upfront R&D investments.
Best Practices for Safe and Efficient Maintenance
Adopt Predictive Maintenance Tools: Vibration sensors and infrared thermometers detect issues before they escalate.
Train Teams for Heat-Specific Scenarios: Conduct drills simulating hydraulic failures at peak temperatures.
Use Climate-Adaptive Fluids: Synthetic hydraulic fluids rated for 100°C+ prevent viscosity breakdown.
Case Studies: Lessons from the Field
Case 1: Port of Singapore Hydraulic Failure
In 2024, a container crane’s seals failed during a 48°C heatwave, spilling 300 liters of fluid and causing a 16-hour shutdown. Post-incident analysis revealed the team had used standard seals instead of high-temp variants.
Case 2: Dubai Solar Farm Success
A contractor using SRP Crane Controls’ thermal-resistant components achieved zero downtime during a 52°C summer, showcasing the value of proactive upgrades.

Conclusion: Mastering the Heat Equation
Maintaining crane controls in hot zones isn’t just about avoiding mistakes—it’s about embracing heat-adaptive strategies. From seal materials to operator ergonomics, every detail matters. As global temperatures rise, partnering with experts like SRP Crane Controls transforms thermal challenges into competitive advantages.