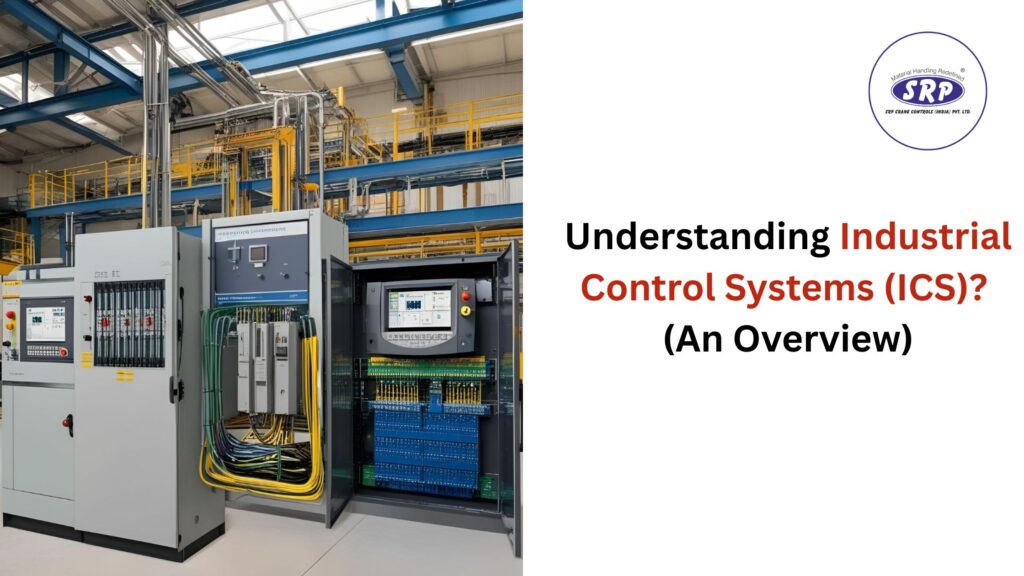
An Industrial Control System (ICS) is a fascinating amalgamation of hardware and software designed to monitor and manage industrial processes. These systems are the backbone of various industries, controlling everything from manufacturing lines to power generation facilities.
This article uncovers the operational mechanics and critical role of ICS in ensuring efficiency, safety, and reliability in modern industrial environments.

What is an Industrial Control System?
ICS systems are essential frameworks for automating processes in industrial infrastructures—from simple machinery operations to complex ones. They enable real-time data collection and control, allowing industries to optimize operations and minimize human error. In earnest to the rise of Industry 4.0 and the Industrial Internet of Things (IIoT), understanding ICS has never been so comprehensible.
The Components of Industrial Control System
At the core of every Industrial Control System is a combination of several key components that work in harmony to ensure effective process control:
- Sensors: These devices collect data on various process variables, such as temperature, pressure, and flow rates. They act as the eyes of the system, providing critical information for decision-making.
- Controllers: Often represented by Programmable Logic Controllers (PLCs), these units interpret sensor data and execute commands based on pre-defined logic. They are the brains behind the operation, making real-time adjustments to maintain desired process conditions.
- Actuators: These components carry out the commands issued by the controllers, adjusting physical variables like opening or closing valves or changing motor speeds.
- Human-Machine Interfaces (HMIs): HMIs provide operators with a visual interface to monitor processes and make manual adjustments when necessary. They are crucial for facilitating communication between humans and machines.
- Data Historians: These systems log all process control activities, enabling analysis and reporting at multiple levels. They help organizations track performance over time and identify areas for improvement.
The integration of these components allows for sophisticated control strategies that enhance operational efficiency and safety across various industries.

Types of Industrial Control System
Industrial Control Systems can be categorized into several types based on their architecture and application:
- Supervisory Control and Data Acquisition (SCADA): SCADA systems are used for controlling dispersed assets across wide geographical areas. They collect real-time data from remote locations, allowing operators to monitor and manage processes from a central location. This is particularly useful in utilities like water treatment plants and electricity distribution networks.
- Distributed Control Systems (DCS): DCS are employed within localized settings such as manufacturing plants. They consist of numerous controllers that manage continuous processes through a centralized system, ensuring coordination across various operations.
- Programmable Logic Controllers (PLC): PLCs are specialized computers designed for industrial automation. They are widely used for discrete control tasks where specific actions need to be executed based on sensor inputs.
Each type of ICS has its unique strengths and is suited for different applications, making them indispensable in sectors such as energy production, chemical processing, and transportation.
Applications of Industrial Control System
The applications of Industrial Control Systems are vast and critical to our daily lives:
- Manufacturing: In manufacturing environments, ICS streamlines production processes by automating machinery operations, reducing downtime, and enhancing product quality through precise control.
- Energy Management: ICS plays a vital role in managing power generation facilities, ensuring efficient energy distribution while maintaining grid stability.
- Water Treatment: Water treatment plants utilize ICS to monitor water quality parameters continuously, automate chemical dosing, and ensure compliance with environmental regulations.
- Transportation: In transportation systems like railways and air traffic control, ICS ensures safe operations by monitoring various parameters in real time.
These applications illustrate how integral ICS is to maintaining the infrastructure that supports modern society.

Benefits of Implementing an Industrial Control System
Implementing an Industrial Control System offers numerous benefits that can significantly enhance operational performance:
- Increased Efficiency: By automating processes, ICS minimizes human error while optimizing resource usage. This leads to higher productivity levels across various operations.
- Safety Improvements: ICS enhances workplace safety by allowing for real-time monitoring of hazardous conditions. Safety protocols can be integrated into the system to prevent accidents before they occur.
- Cost Reduction: Over time, automation through ICS can lead to substantial cost savings by reducing labor costs, minimizing waste, and improving energy efficiency.
These advantages make a compelling case for organizations looking to modernize their operations through advanced control systems.
Challenges Facing Industrial Control System
Despite their benefits, several challenges confront Industrial Control Systems today:
- Cybersecurity Threats: As ICS becomes increasingly connected through IIoT technologies, they become more susceptible to cyberattacks. Many ICS were not designed with cybersecurity in mind. The increase in the number of cyber incidents on ICS networks is a reality the industry can no longer ignore. The infamous Stuxnet incident serves as a stark reminder of how vulnerable these systems can be if not adequately protected.
- Integration Issues: Integrating new ICS with existing infrastructure can pose significant challenges due to compatibility issues between legacy systems and modern technologies.
- Skill Gaps: There is a growing need for skilled professionals who can effectively manage and maintain these complex systems. The lack of training programs tailored specifically for ICS contributes to this skills gap.
Addressing these challenges is crucial for organizations aiming to secure their operations against potential threats while maximizing the benefits offered by modern control systems.
Future Trends in Industrial Control Systems
The future of Industrial Control Systems is promising as technological advancements continue to reshape the landscape:
- Advancements in Technology: Emerging technologies such as AI and machine learning are being integrated into ICS to enhance predictive maintenance capabilities. This allows organizations to anticipate equipment failures before they occur, reducing downtime significantly.
- Sustainability Focus: As industries strive for sustainability, ICS will play an essential role in optimizing resource usage and reducing environmental impact through smarter process management5.
- Industry 4.0: The shift towards Industry 4.0 emphasizes connectivity between machines and data-driven decision-making processes. This evolution will see an increased reliance on advanced analytics within ICS environments.
These trends indicate that understanding ICS will be vital for anyone looking to thrive in the future industrial landscape.
Conclusion
In summary, understanding Industrial Control Systems is beneficial and essential for anyone passionate about technology’s role in industry today. From their critical components to their diverse applications across sectors like manufacturing and energy management, ICS represents a convergence of innovation that drives efficiency and safety in our increasingly automated world.
As we move forward into an era marked by rapid technological advancements like IIoT and AI integration, staying informed about developments within this field will empower individuals and organizations alike. For those intrigued by this domain or looking for tailored solutions that align with their operational needs, engaging with experts at SRP Remote could provide invaluable insights into harnessing the full potential of Industrial Control Systems.