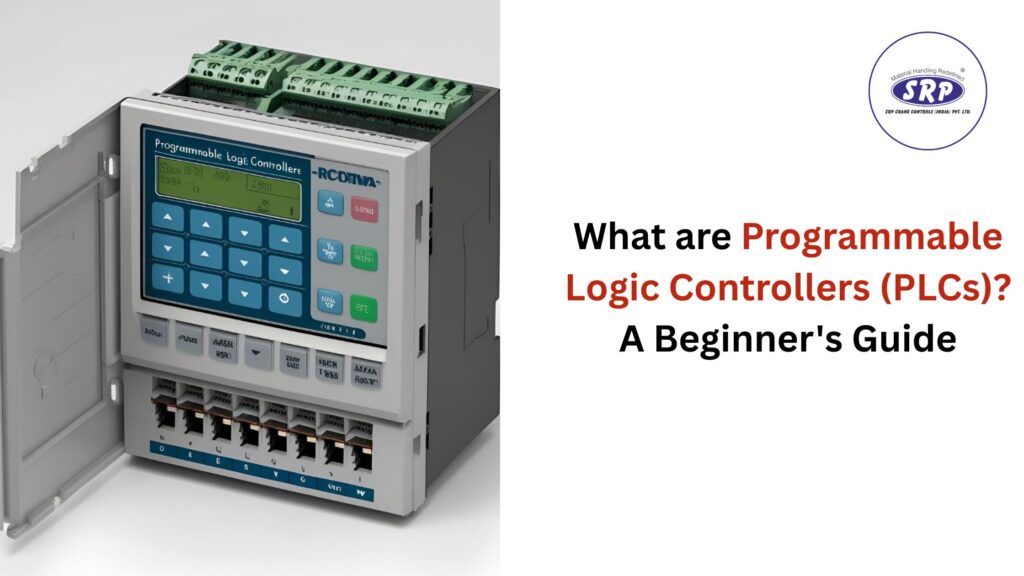
Programmable Logic Controllers (PLCs) have revolutionized the landscape of industrial automation. These robust devices are designed to control machinery and processes in real time, making them indispensable in various sectors. The journey of PLCs began in the late 1960s when they were introduced as a solution to replace hardwired relay systems. Today, they stand at the forefront of modern manufacturing, enhancing efficiency and reliability across industries.
What is a Programmable Logic Controller (PLCs)?
At their core, PLCs are specialized computers that monitor input devices—such as sensors and switches—and process this information according to user-defined programs. The output is then directed to control devices like motors, actuators, and alarms. This capability allows PLCs to automate simple machine operations to complex production line processes.

How Programmable Logic Controllers (PLCs) Work
Understanding how PLCs function is crucial for anyone interested in industrial automation. A PLC operates through a cyclical process known as the scan cycle, consisting of three primary phases: input, program, and output.
Input Scan: The PLC reads the status of all input devices.
Program Scan: The PLC executes the user-defined program based on the input status.
Output Scan: The PLC updates the output devices according to the results of the program scan.
This continuous loop allows PLCs to respond instantly to changes in input conditions, ensuring precise control over machinery and processes. Unlike general-purpose computers, which can perform various tasks, PLCs are optimized for real-time control, making them ideal for industrial applications where timing is critical.

Types of Programmable Logic Controllers (PLCs)
There are several types of Programmable Logic Controllers (PLCs), each tailored for specific applications:
- Compact PLCs: These are designed for smaller applications where space is limited. They integrate all components into a single unit, making them easy to install and maintain.
- Modular PLCs: Offering scalability and flexibility, modular PLCs allow users to add or remove I/O modules based on their specific needs. This adaptability makes them suitable for larger, more complex systems.
- Soft PLCs: These software-based controllers run on standard computer hardware. They provide the flexibility of traditional PLCs while leveraging the processing power of modern PCs.
Each type has its unique advantages, making it essential for users to choose based on their specific requirements.

Applications of Programmable Logic Controllers (PLCs)
The versatility of Programmable Logic Controllers (PLCs) is evident in their widespread use across various industries:
- Manufacturing: PLCs automate assembly lines, controlling everything from robotic arms to conveyor belts.
- Water Treatment: They manage filtration and chemical dosing processes, ensuring a safe water supply.
- Oil and Gas: In this sector, PLCs control drilling operations and monitor safety systems.
- Building Automation: They regulate heating, ventilation, air conditioning (HVAC), lighting systems, and security features in commercial buildings.
Real-world case studies highlight the effectiveness of PLCs in improving operational efficiency and reducing downtime. For instance, a manufacturing plant that integrated a modular PLC system reported a 30% increase in productivity due to enhanced automation capabilities.
Benefits of Using Programmable Logic Controllers (PLCs)
The adoption of Programmable Logic Controllers (PLCs) offers numerous advantages that contribute to their popularity in industrial automation:
- Enhanced Efficiency: By automating repetitive tasks, PLCs reduce human error and increase production rates.
- Flexibility: Changes can be made quickly through software updates without needing extensive rewiring or hardware modifications. This adaptability is crucial for industries that must respond rapidly to changing demands.
- Reliability: Built to withstand harsh conditions—such as extreme temperatures and vibrations—PLCs are designed for longevity and minimal maintenance. Their rugged nature ensures they operate consistently over extended periods.
- Real-Time Operation: The ability to process inputs and outputs in real-time allows for immediate responses to changes in operational conditions, which is vital for applications requiring precise timing.
- Data Management: Modern PLCs can collect and analyze data from various sensors and devices. This capability enables operators to monitor performance trends and make informed decisions based on real-time insights.

Challenges and Considerations with Programmable Logic Controllers (PLCs)
While there are many benefits associated with Programmable Logic Controllers (PLCs), there are also challenges that users should be aware of:
- Initial Investment Costs: Although PLCs can lead to long-term savings through improved efficiency, their upfront costs can be significant, particularly for small businesses.
- Complex Programming Needs: While programming languages like ladder logic are user-friendly for basic tasks, more complex applications may require advanced programming skills or extensive algorithms.
- Maintenance and Upgrades: As technology evolves, maintaining older systems can become challenging. Upgrading software or hardware may require careful planning to avoid disruptions in operations.
Despite these challenges, the overall benefits often outweigh the drawbacks when implementing a well-planned PLC system.

Conclusion
In conclusion, Programmable Logic Controllers (PLCs) play a pivotal role in modern industrial automation by providing reliable control over complex processes. Their ability to enhance efficiency while adapting quickly to changing needs makes them invaluable across various sectors. For passionate amateurs looking to delve deeper into this field, understanding the fundamentals of PLC technology opens up exciting opportunities for innovation and improvement in industrial processes.